Emser Tile is America’s leading designer, marketer, and producer of world-class tiles and natural stones. The company’s headquarters are based in Los Angeles, California, USA. Emser is one of the most complete sources for interior and exterior housing decorative materials, including ceramics, metal, glass, quarries, stones, and customized-made products, thanks to its unmatched customer service and diverse product range.
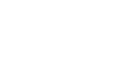
Hours delivered back to the business
Customer Satisfaction
Success rate of completion
Total Team Experience
The Challenge
Emser Tile has a goal of improving its warehouse management capabilities through the use of NetSuite Oneworld, the incorporation of innovative supply chain modules, and the application of advanced warehousing technologies.
Emser Tile sought to implement advanced transportation modules to improve delivery times, cut costs, and optimize route planning. The key objective was to build a more flexible and responsive supply chain that could effectively fulfill the rising demand for their goods while still being economical.
Emser Tile experienced a number of difficulties in managing their supply chain, including problems with inventory visibility and ineffective warehouse management.
Order fulfillment and operational effectiveness were hindered by manual and inefficient warehouse operations.
The project’s goal was to give Emser Tile an identical, real-time perspective of all of their supply chain operations working globally. By doing so, we aim to enable them to track inventory levels, demand trends, and production schedules globally.
Solution provided by EPIQ
Emser Tile partnered with EPIQ, a leading provider of NetSuite ERP solutions, and helped the company create innovative warehousing and shipping modules for their current system. Real-time monitoring of stock across their global network was made possible by their superior warehousing capabilities, which improved inventory management and decreased the likelihood of shortages. The technology also improved the process of picking and warehouse layout procedures, which raised productivity and decreased costs related to operations.
NetSuite advanced transportation module enables the Emser Tile to monitor and optimize its various shipping routes; it aids in reducing transportation lead times and minimizes the organizational cost. This improved the ability to fulfill client supply demands.
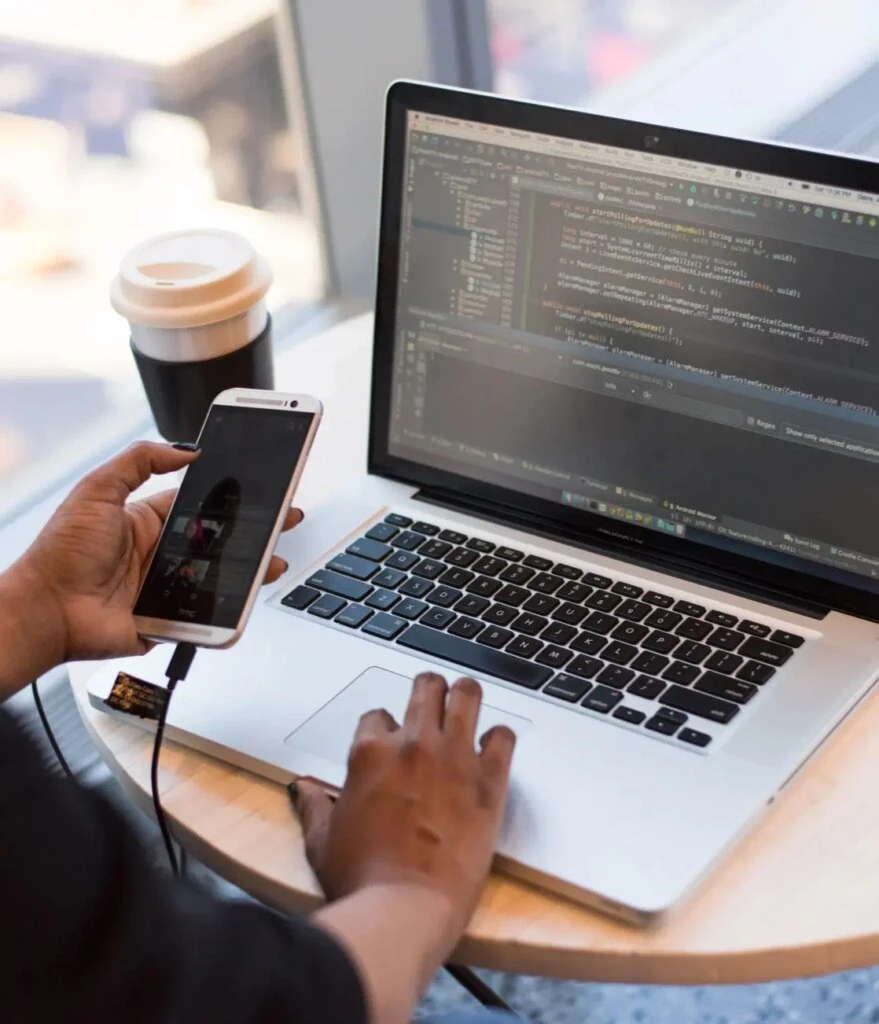
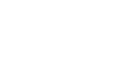
The Results
- The primary objective was to develop a supply chain that was more responsive and adaptable so that it could efficiently meet the growing demand for their products.
- Developed innovative modules for warehousing and shipping into their current system.
- Emser Tile uses this to track and optimize its multiple routes of shipping, which reduces the waiting period for transportation and lowers organizational costs.
- To speed up deliveries, save expenses, and enhance route planning, the company intended to deploy a modern transportation module.
- Emser Tile's multifaceted operations demanded effective management of diverse ERP modules, leading to increased complexity in workflows and processes.